What is deep-drawing?
Emprotec produces parts by cold forming sheet metal.
This means transforming a flat sheet of metal into a three dimensional hollow part. It consists of forcing a sheet of metal progressively into a forming die by using a press.
At each stage the part is formed step by step more deeply into the die, this is what we call deep drawing.
The aim is to shape parts with deep cavities and at the same time preserving their structural integrity.
This type of forming is carried out on a transfer press fitted with a drawing tool which consists of :
- A punch which is in the shape of the inside of the part to be produced
- A forming die which supports the material and gives it the final outside shape
- A blank holder which presses the blank against the outside of the die to ensure a regular flow of metal
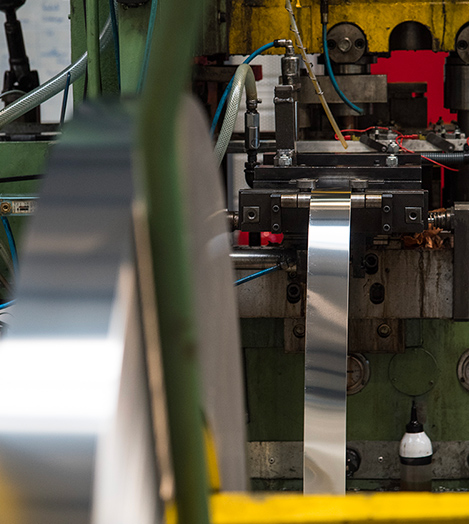
Emprotec uses transfer presses which are fitted with lateral gripper rods, this means that all the drawing operations required for the end product can be carried out simultaneously.
The entire drawing process can be carried out on a single press.
The main advantages are, first of all, that the part is maintained in the best position between the different operations, (compared to a line of presses) and that there is a high speed of output.
These relatively high rates of production can lead to heating of both parts and tooling, a water-based oil spray is used to absorb the calories.
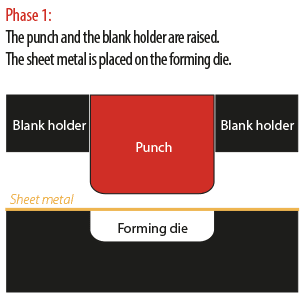
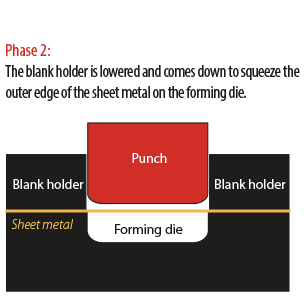
Phase two :
The blank holder is lowered and comes down to squeeze the outer edge of the sheet metal onto the forming die.
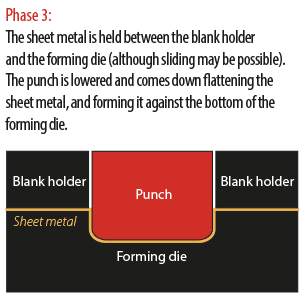
Phase three :
The sheet metal is held between the blank holder and the forming die (although sliding may be possible).
The punch is lowered and comes down flattening the sheet metal, and forming it against the bottom of the forming die.
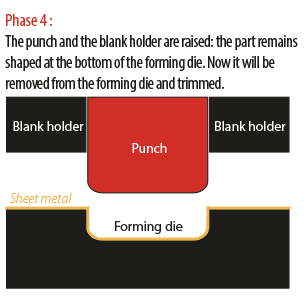
Phase four :
The punch and the blank holder are raised: the part remains shaped at the bottom of the forming die. It only remains to remove it from the forming die and trim it.
Advantages of the process
A process which gives a high level of precision in dimensions and at the same time reduces costs.
Deep-drawing has many positive aspects, not only in terms of cost but also in quality of parts, in particular thanks to the wide range of material which can be transformed, and the very nature of the process which ensures rational production, avoiding costly additional operations which may be necessary with other techniques.
With this technique the main advantage is ensuring relatively low cost price and very high rates of production. Emprotec’s production capacity varies from 900 to 1 800 parts per hour depending on size and complexity of the parts.
Forming of the sheet metal results in strain-hardening which gives the finished part higher characteristics than the blank. These higher characteristics mean that it is possible to make parts lighter. Surface quality of raw parts after drawing is distinctly higher than that of cast parts. The visual aspect of deep-drawn parts in therefore much better and finishing work such as polishing is reduced and, above all, less costly.
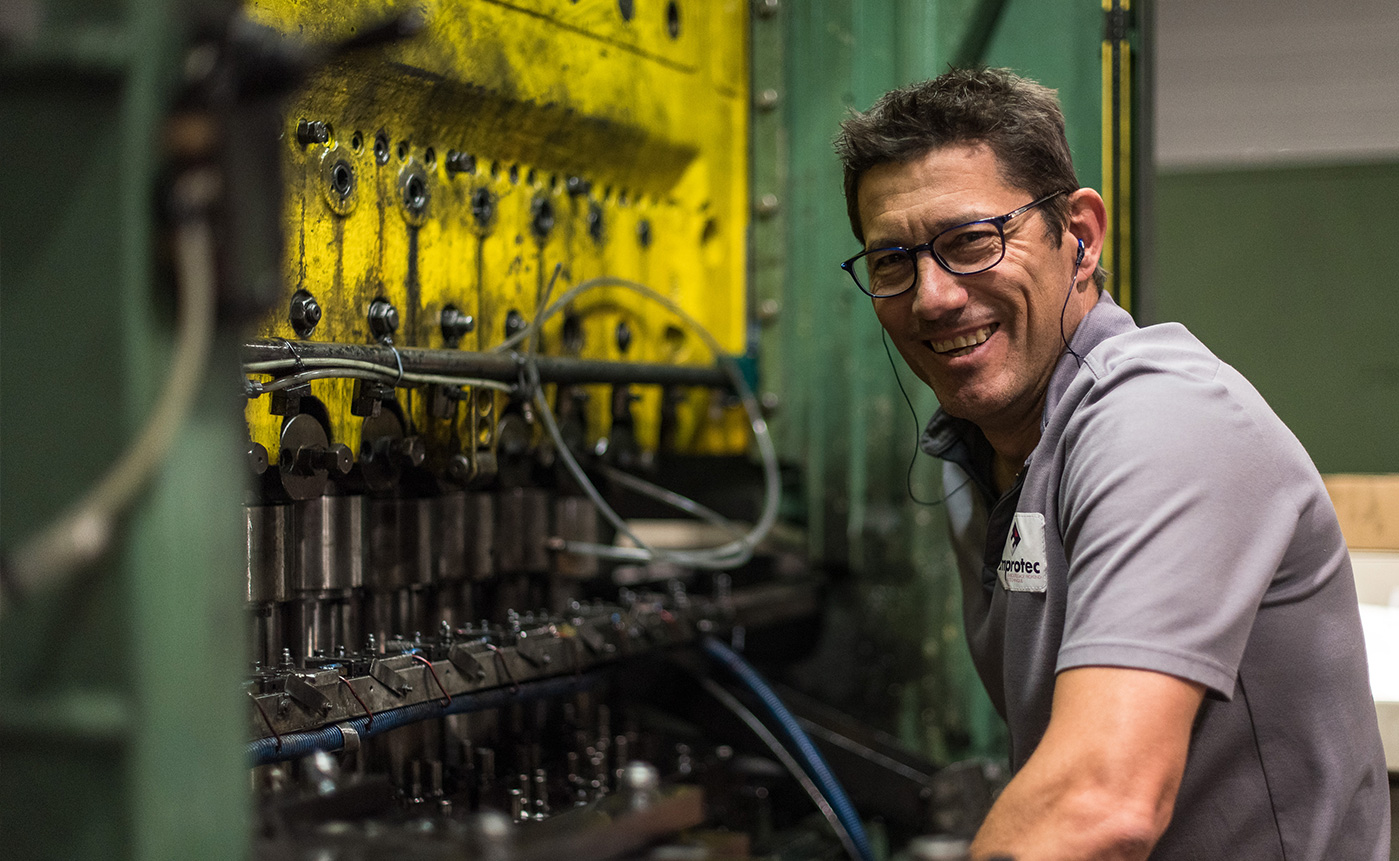
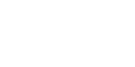
Materials
Different materials to meet each different need.
Emprotec uses different materials depending on the technical specifications given by the client and the recommendations of the R&D department.
Soft steel
By using modern laminating techniques it is possible to obtain very thin steel sheets with a clean smooth surface, a regular surface and a range of mechanical characteristics which are compatible with the demands of deep-drawing.
This sheet metal is divided into three categories:
- Sheet metal for standard production
- Sheet metal for drawing
- Sheet metal for special drawing
Cooper
When it is not alloyed with another element red copper has excellent qualities for extra deep-drawing which are often better than those of brass or special steel.
Stainless steel
The excellent mechanical characteristics of stainless steel mean that it is highly suitable for shaping. The high ratio between mechanical resistance and material weight and the unique characteristics for elongation and strain-hardening make stainless steel a solution for a lot of complex shapes.
Brass
The most common are 60/40 and 72/28.
This grade (72% copper and 28% zinc) is used for the production on cartridges and sleeves and does not require annealing.
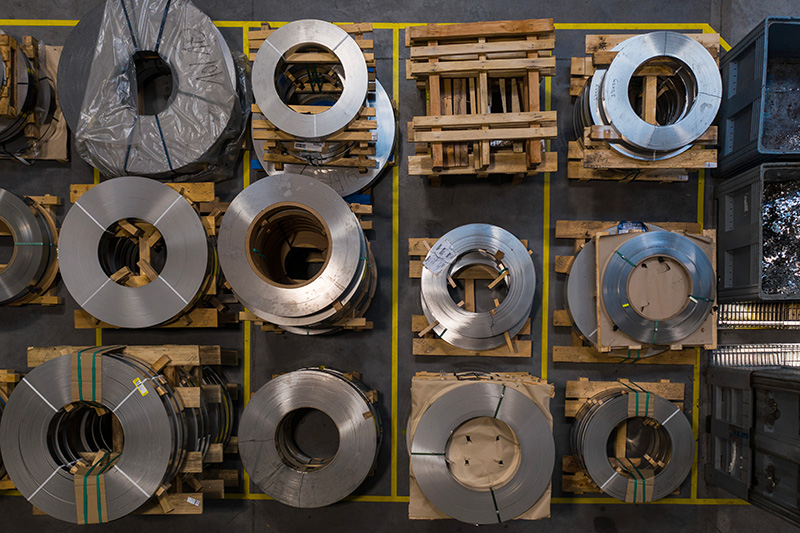
Our References
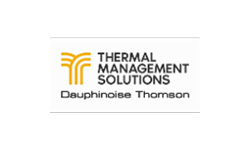
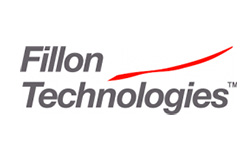

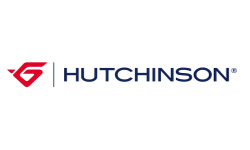
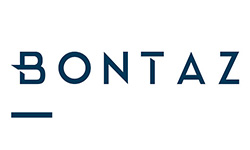
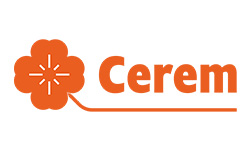
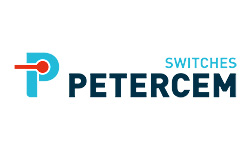
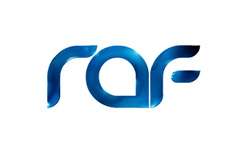
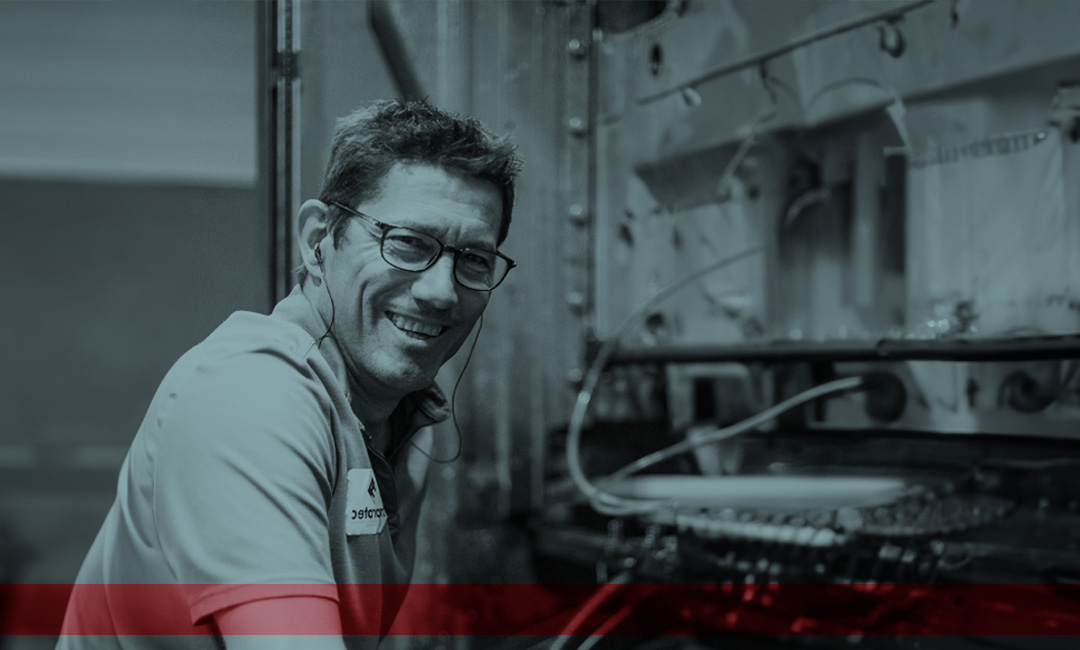
Would you like
to learn more?
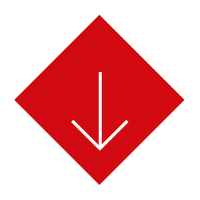
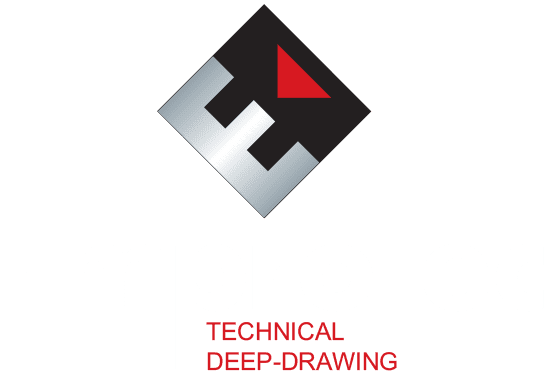
Your trusted partner in deep drawing, Emprotec supplies you with high quality technical parts, bringing together expertise, innovation and meeting clients’ demands.
Parc d’activités Alpespace
401 Voie Galilée
73800 Sainte-Hélène-du-Lac
France
Regional Support: